Continuing our series on navigating ink-related food safety standards
We’re publishing dedicated blogs that explore each standard and explain how our ink management solutions can help you comply with them. See our previous blogs on housekeeping and cleaning, hazard analysis and risk management, record keeping, traceability, equipment maintenance, housekeeping and cleaning, waste and waste disposal and good manufacturing practices.
This is a blog about the eighth standard, calibration and control of measuring devices.
In food packaging printing, accurate measuring and monitoring devices are essential for ensuring product safety and quality. Common tools include weighing scales, viscosity meters, pH meters, temperature/humidity monitors, and colour measurement devices. In ink dispensing, calibration involves two key areas: the entire system (software, controls, pumps, valves) and the weighing scale, which ensures precise ink dispensing. Both levels are critical for consistent colours and compliance with food safety standards.
We will cover the relevant requirements of the GFSI-recognized schemes (BRCGS, SQF, and FSSC 22000), and our products and services that help you to comply.
Calibration requirements in the three food safety management schemes
The criteria for calibration and control of measuring devices can be found in:
- Section 5.5 of the BRC Global Standard (BRCGS) for Packaging Materials
- Sections 1.13 of FSSC 22000 (Food Safety System Certification)
- Section 13.2.3 of Safe Quality Food (SQF).
To ensure accurate and reliable monitoring of food safety and regulatory compliance, all three standards require the following key actions:
Equipment identification and control
Food safety-critical measuring and monitoring devices must be clearly identified, listed in a register, and protected from damage or unauthorized adjustments. The register should include:
- Equipment ID and location
- Calibration frequency, method, and due dates
- Acceptance criteria and corrective actions for non-compliance
Calibration practices
Calibration must be performed:
- At defined intervals, based on risk or regulatory/manufacturer guidance
- By trained internal staff or qualified external providers
- Using national or international standards when possible, or with justified alternative methods if not
Calibration records must be documented, securely stored, and accessible.
Non-conformance and corrective actions
Procedures must be in place for handling equipment found to be out of calibration. These include:
- Assessing potential product impact
- Isolating, quarantining, or rechecking affected products
- Performing root cause analysis and implementing corrective and preventive actions
Dispensing system calibration and machine learning: A.I. your inks!
In our blog Ink dispensing: the basics, we explain that a high-precision weighing scale is at the heart of every GSE ink dispensing system – critical for achieving accurate and consistent ink formulations. Our gravimetric dispensers are built around a sophisticated system design – an interplay of advanced machine controls, electronics, pneumatics, pumps, dosing valves, and the weighing scale.
In gravimetric ink dispensing, achieving precise ink weights depends on understanding two key phases of movement: flow and fall.
- Flow refers to the active stage where ink is pumped through valves into the mixing container.
- Fall occurs after the pump stops and the valves close.
Using machine-learning capability, our software optimizes the flow and fall parameters, based on environmental factors, such as temperature – during both dispensing and calibration. This ensures the precise volume of ink is dispensed as fast as possible, even when a change in atmospheric conditions affects the ink’s rheological properties.
System calibration can take place both via software and mechanically. Our valves are engineered to accurately dispense coarse flows, fine flows, and drops. In the system calibration screen of GSE Ink manager, up to five different flow rates and two different drop levels can be selected for each base component. To test dispensing accuracy, a bucket is placed on the scale, and ink is dispensed for precisely ten seconds at each of these flow rates. In each case, the flows and falls are measured automatically. For drops, the drop flow, valve open time, and drop size are also precisely measured and automatically calibrated.
If the new parameters are within specification, the operator can choose to store these values in the system. If not, a mechanical calibration must be performed. During this process, the fine flow of the dosing valve is mechanically adjusted using specialized tools, followed by a new software-based calibration to verify and fine-tune the results. If the dosing valve cannot be calibrated to meet specifications, it must be serviced (with a revision procedure) or replaced.
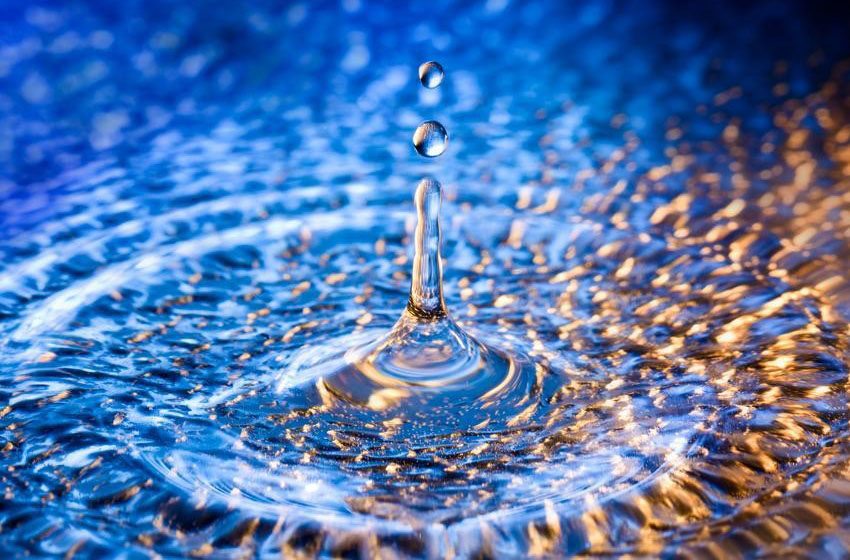
Ink dispenser valves are engineered to accurately dispense coarse flows, fine flows, and drops of inks and varnish.
During the installation of a new dispensing system – or in the event of a reinstallation or ink change – our technician performs a comprehensive system calibration, both software-based and mechanical. This also applies to visits as part of a service contract or as a corrective action.
After commissioning, there are several reasons to perform a calibration of an individual component. This is typically done after replacing or servicing a dosing valve or pump, in the case of suspected issues, or as part of a defined interval to meet the food safety requirements described above.
The extent to which calibration is performed by in-house personnel depends on the customer’s internal policy and capabilities. Some customers choose to have all calibration activities carried out exclusively by GSE. Others handle only the software-based calibration themselves, or choose to perform the mechanical calibration under the supervision of our remote support desk engineers. Larger companies with a dedicated maintenance department may opt to do everything in-house – including valve and pump replacement or revision, and full calibration procedures. Our GSE technicians are available to train your staff in these procedures, ensuring a safe, compliant, and efficient operation.
Regardless of the chosen approach, to comply with GFSI requirements, your calibration policy must be clearly documented.
Calibrating the weighing scale
If you have a GSE installation, we can also provide a weighing scale calibration service, to ensure your system continues to operate with optimal accuracy and compliance. Using certified weights and a standardized calibration report, our technician checks key functions such as zero setting, tare, display stability, and repeatability. Applied loads are measured at five points across the scale and compared to the scale readings, to confirm they fall within the defined tolerance. If discrepancies are found, corrective actions are identified and, whenever possible, carried out on-site.
For customers with a service contract, we provide this calibration service free of charge during one of the scheduled visits, as part of the agreement.
Conclusion: keep calibration under control
Accurate calibration isn’t just a technical detail – it’s a core requirement for meeting GFSI standards and ensuring safe, compliant food packaging. Whether you rely on GSE for full calibration support or choose to manage it in-house, your procedures must be clearly defined, properly documented, and consistently applied.
At GSE, we’re here to support you with the tools, services, and expertise to help you stay compliant and confident. From intelligent system calibration features in GSE Ink manager to on-site weighing scale checks and tailored staff training – we’ve got you covered.
Further reading on the InkConnection blogsite
Need help setting up or validating your calibration procedures?
Get in touch with our experts at info@gsedispensing.com or visit www.gsedispensing.com to learn more about our service options and support.